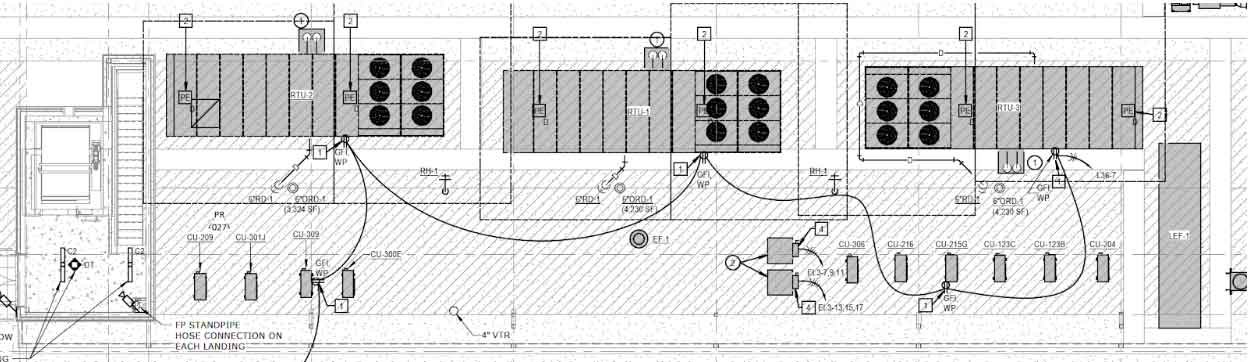
By Kevin Player
Unraveling a Mystery with Rooftop Units
in Building Commissioning
In the realm of commissioning, I've found that each project is akin to a cryptic puzzle waiting to be unraveled. After years of experience, I've come to realize that commissioning (CXing) is a labyrinth of mysteries. Like an investigator embarking on a new case, you're never certain what enigmas will unfold, yet you're assured that the process of deciphering them will be enlightening.
A recent case study underscores this analogy, detailing the intriguing challenges encountered during the commissioning of a three-story lab and office building, particularly regarding irregular readings from the rooftop units (RTUs).
The Mystery
A three-story laboratory and office building was purposefully designed so that each floor was serviced by a dedicated packaged rooftop unit (RTU). These units served either the laboratory supply valves with hot water reheat coils or hot water reheat terminal units for non-lab spaces. The rooftop plan detailed the general layout for each RTU, leaving the contractor to place the three units strategically between a penthouse stairwell and a screen wall.. However, during the commissioning (CXing) process, a discrepancy emerged. The outside air (OA) sensor for RTU-2 registered 35F and RTU-1 recorded 31F, while the actual outside air temperature was 23F.
After delving into this mystery, it became clear that the warm (~70F) building air being exhausted was getting drawn back into the outside air intake, where the OA sensor was located. This issue could be attributed to a couple of factors: firstly, RTU-2 was installed approximately 2 feet from the penthouse wall (see picture below), less than the recommended minimum distance of 6 feet stipulated in the installation manual, facilitating the exhaust air to be recirculated back into the outside air intake. Conversely, RTU-1 was installed at a distance of 6 feet 8 inches from RTU-2, adhering to the manufacturer's recommendations. This led to the question: why was the OA sensor on RTU-2 compromised by the warm exhaust air if it was within the recommended distance?
Further investigation revealed that the outside airflow station had not been calibrated for RTU-1 or 2, and each was measuring about 50% higher than the actual airflow rate. This miscalibration led to higher energy consumption to condition the excess outside air and increased the possibility of exhaust air being recirculated into the outside air intake. Calibrating the airflow stations helped reduce the OA sensor inaccuracy somewhat, but only by about 2F. Consequently, the readings on RTU-2 were still off by 10F, and RTU-1 by 6F.
The engineer's control sequence had directed the operation of the return fan for each RTU, using a 5-10% return fan offset with barometric relief damper control to maintain building pressure. However, the engineer had not provided a recommended building pressure setpoint, and each floor was consistently negatively pressurized at around -0.08”, which indicated the return fan speed for each RTU was too high, thereby creating excessively high exhaust airflow. The technician correctly set the offset to 5% during RTU startup, as per the engineer's recommendation, but it had to be increased to a range of 30-40%, depending on the RTU, to maintain proper building pressure and reduce the excessive exhaust airflow.
Eventually, the return fan offset control was discontinued, and the RTU was reconfigured to control the return fan to a +0.05” building pressure setpoint. A building pressure sensor was also installed on each floor. These changes allowed each RTU to maintain appropriate building pressure for its corresponding floor across all operating conditions, including when the RTUs entered economizer mode. At OA temperatures below 50F, the OA sensor was now reading accurately. However, when RTU-2 entered economizer mode (set to 60F to optimize energy savings and maintain stable lab conditions), the outside air damper opened fully; thereby correctly causing the return fan speed to increase. This resulted in higher exhaust airflow and once again compromised the outside air sensor, albeit only by approximately 3-5F at an OA temperature of about 55F. Nonetheless, the discrepancy wasn't substantial enough to disable the economizer mode.
About Kevin Player
Kevin Player is a dynamic leader and the driving force behind the commissioning and Measurement & Verification (M&V) programs at Millig Design Build. As the Director of Project Performance, he spearheads these initiatives on a national scale, ensuring optimal project outcomes across the organization. With an impressive 15-year track record in testing, verifying, and troubleshooting electronic and HVAC systems, Kevin possesses a deep understanding of the intricacies involved in achieving peak performance and energy efficiency.
OUR SOLUTIONS
Heating, ventilation, and air conditioning
Smart meters and building controls
On-site solar and other renewable energy systems
LED lighting retrofits
Building envelope improvements
Water systems
CHP-Cogeneration
And more
CONTACT US