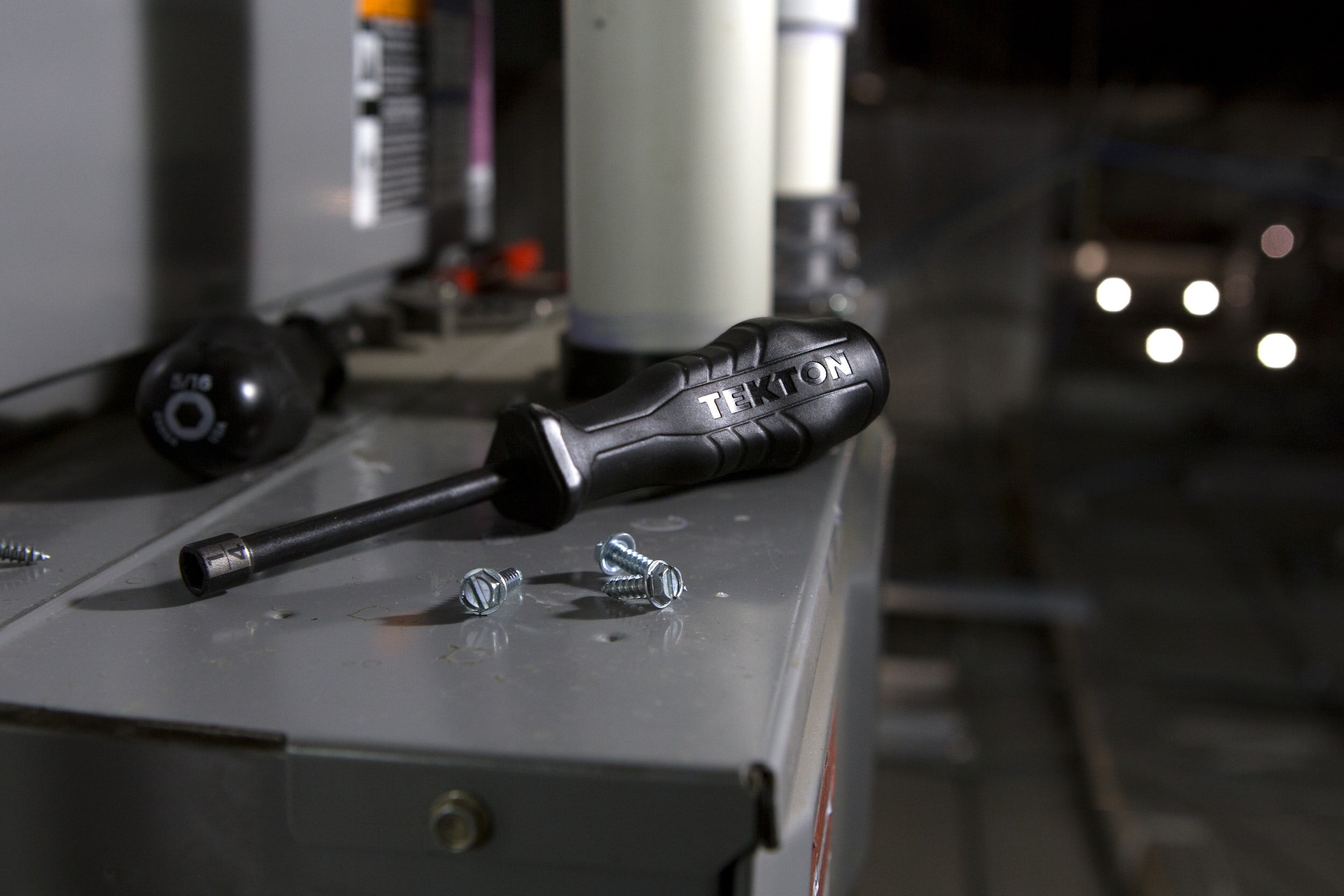
By Josh Slocum, PE
How to Deploy a Preventative Maintenance Strategy for your Buildings
If you’re responsible for keeping building facilities in tip-top shape, no doubt you’re facing increasing pressure to reduce costs all while ensuring uptime and occupant comfort and safety. Understanding equipment life cycle and having a comprehensive maintenance strategy in place are key to maintaining the efficiency and effectiveness of your facilities’ mechanical systems and reducing your organization’s risk for costly repairs. Before we dive into how to deploy a comprehensive facility maintenance strategy, let’s first review the three main categories of maintenance strategies: reactive, preventative, and predictive.
Reactive Maintenance
Sometimes referred to as fix-on-fail, reactive maintenance occurs when something breaks. So, it’s not really a ‘strategy’ at all. (It’s more like driving your car until a belt fails.) And while going this route may be appealing to those concerned with upfront costs, the long-term impacts of a reactive maintenance strategy are far more damaging. Why? Unless your facility has replacement parts for every possible piece of equipment — and technicians on staff who can work on them 24/7 — you’re likely to experience significant downtime and costly repair, especially with today’s supply chain challenges.
Preventative Maintenance
The intent of a preventive maintenance strategy is to prevent costly equipment failure before it occurs. This is achieved by inspecting and servicing equipment on a calendar- or usage-based schedule, according to manufacturer recommendations. (To keep with the car analogy, it’s like checking your tire pressure and having regularly scheduled oil changes.)
Calendar-based maintenance is the most common type of preventive maintenance; depending on the type of asset, it can be deployed weekly, monthly, quarterly, or annually.
Usage-based maintenance relies on meter readings that tell maintenance staff when specified measurements have been reached.
Benefits of employing a preventative maintenance plan include:
Less downtime and closures
Longer equipment life expectancy
Less time spent working on equipment outside regularly scheduled hours
Equipment that operates more efficiently
Reduced risk of accidents and safety violations
Lower utility costs
There are disadvantages as well: higher up-front costs, greater labor intensity, and the potential for over-maintenance. In fact, according to ARC Advisory Group’s Enterprise Asset Management and Field Service Management Market Study, as much as half of every dollar you spend on preventive maintenance could be wasted on allocating labor and parts to mechanical assets that are not in immediate need of maintenance. That’s why it’s important to weigh and balance failure prevention activities, which we will show you how to do later in this post.
Steps to Deploying a Preventative Maintenance Strategy
STEP ONE: TAKE INVENTORY
The first step is to develop a cloud-based spreadsheet that includes a full inventory of your equipment and any tools or resources available to assist your maintenance staff. (There is software available that can do this as well, but for the purposes of this post, we’ll use Google Sheets, which can be accessed by your entire maintenance staff in real-time.)
[DOWNLOAD OUR SAMPLE EQUIPMENT INVENTORY SPREADSHEET]
Within this Google Sheet, you’ll also want to populate information about your staff and their roles and specialties. Being able to communicate how your staff is able (or unable) to execute the full preventative maintenance needs of your facilities is crucial to determining what gaps you will need to fill with service agreements or training. It’s also a great way for staff nearing retirement to pass along knowledge so that remaining staff can benefit from their wisdom and experience.
STEP TWO: PRIORITIZE MAINTENANCE NEEDS
Once you’ve finished compiling your inventory, it’s time to conduct a criticality analysis. A criticality analysis is a weighted matrix you will use to prioritize maintenance planning. It’s based on an asset’s level of criticality and preventative maintenance needs.
First, rate the seriousness of an event based on the factors below (1 being least serious):
Health and safety implications of the failure of equipment
Downtime to repair equipment
The energy it takes to repair equipment
Cost to repair equipment
Next, weigh the criticality of individual preventative maintenance tasks for each piece of equipment, which can be found in your O&M manual. (Below is an example of preventative maintenance tasks for an air handler.)
Change air filter
Clean fan blades
Verify fan RPM
Tighten bearing collar set
Set screw on fan shaft
Test and tighten damper
Linkages
Clean dampers
Lubricate damper connections
Clean condenser & evaporator coils
Check refrigerant level
Clean condensate pan
Replace worn belts
Align and resheave belts
Vacuum and clean unit
As you can see in this simplified criticality analysis example, there are several tasks with very low criticality. This doesn’t mean these tasks should be ignored. It means that these tasks should be performed less frequently than tasks with a higher value of criticality.
STEP THREE: FILL IN STAFF KNOWLEDGE GAPS
If your maintenance department does not have the time, tools, or experience needed to perform preventative maintenance for a particular piece of equipment, a service agreement with a mechanical contractor should be considered.
When investigating service agreements, it’s important to be specific concerning the work you need done. You’ll also want to request a comprehensive report of maintenance completed while the mechanical contractor is onsite. This report should contain concrete data on the key performance indicators of the equipment being serviced, including pressures, temperatures, and combustion analysis.
STEP FOUR: EXECUTE YOUR PLAN
Create a standard procedure and checklist for each piece of equipment with tasks for each season or predefined usage measurement, and execute it according to plan.
Predictive Maintenance
The last maintenance strategy we will cover is predictive maintenance. At its core, predictive maintenance uses monitoring sensors, artificial intelligence, and automation system feedback to predict the failure of parts and processes using pre-programmed defect observation triggers.
The goal of predictive maintenance is to first predict when equipment failure could occur and then prevent the failure through regularly scheduled and corrective maintenance.
Examples of Predictive Indicators:
Controls: Performative curve comparison, equipment oscillation, failure to meet setpoint
Mechanical: Differential pressure, short-cycling, motor temperature, bearing temperature
Scheduling: Equipment performance drift
Safety: Severe weather, critical parameter monitoring
There are numerous platforms that provide predictive maintenance services:
Standalone platforms that integrate with existing building automation systems
Optional add-ons designed by digital controls software manufacturers
Computerized maintenance management software or enterprise asset management
If you’re considering deploying a predictive maintenance strategy, it’s important to note that predictive maintenance systems have a much higher setup cost and typically require subscriptions with annual fees. They also have additional sensors that need to be maintained and calibrated, which requires considerable training for maintenance personnel.
About Equipment Life Cycle
No equipment lasts forever — no matter how well it is maintained. That’s why strategic life cycle management is vital to not only going beyond the fix-on-fail mentality but also to reap the full benefits of your assets for as long as possible.
The Four Key Stages of Equipment Life Cycle
STAGE ONE: PLANNING
The first stage, and the one most forgotten until equipment failure, is planning. Planning for equipment failure should begin as soon as the operational and maintenance phase begins and if you haven't started planning for the eventual renewal or disposal of your current equipment.
STAGE TWO: PROCUREMENT
The second phase is procurement. After your organization budgets for and purchases an asset, you add it to your equipment inventory spreadsheet.
[DOWNLOAD OUR SAMPLE EQUIPMENT INVENTORY SPREADSHEET]
STAGE THREE: OPERATION
The third phase is the operation and maintenance period. During this time, you are maintaining your asset on a calendar- or usage-based schedule, according to manufacturer recommendations.
STAGE FOUR: DISPOSAL
The final phase is the proper disposal of an asset when it’s reached the end of its useful life. (ASHRAE provides a table of the estimates of life expectancy for most types of equipment.) From this list, you can determine the equipment to be considered for replacement.
And then, the equipment life cycle starts again.
About Josh Slocum, PE
As a Project Development Engineer, Josh provides technical oversight that ensures high-performance facility improvements. He has exceptional aptitude in engineering applications and is an experienced manager who has earned the respect of coworkers and clients alike. Josh has a background in mechanical engineering and commissioning. This diverse background allows him to view projects through multiple lenses, providing technical oversight that ensures high-performance facility improvements.
OUR SOLUTIONS
Heating, ventilation, and air conditioning
Smart meters and building controls
On-site solar and other renewable energy systems
LED lighting retrofits
Building envelope improvements
Water systems
CHP-Cogeneration
And more
CONTACT US